How A:B Stand is made
We couldn’t reveal the designing and manufacturing process of About:Blank Stand due to the patent issue. We have finished the process by the end of August, and are very happy to finally share it with you.
It started about two years ago while I was still working for a Helsinki-based design consultancy as a concept designer, having meeting with the clients outside the office premises. So I had to use laptop although I had chronic pain on back of my neck, and so I was looking for a stand to use with extra input devices. After the launch of About:Blank Notebook in September 2009 I have been trying to persuade Seunghoon and Hyunsun for working on this. They did not like the idea of making another “peripherals” as they come and go as technology always evolves faster than we think.
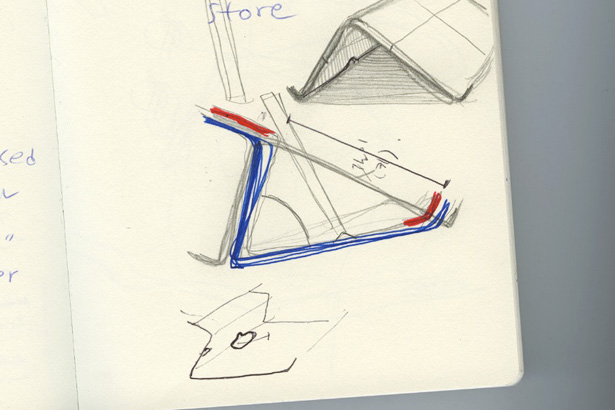
One of the first sketches of the current design
I found the plywood pressing technique fascinating as it makes products a lot like furniture that one can use for a long time and grow old together – emotionally durable, if you will, as long as there are people using laptops and tablet PCs. This new furniture will sell even in the 2nd hand shops and antiques for the next people just like tables and spoons. Seunghoon and Hyunsun eventually bought my argument, and after many trials and errors, we’ve come across the current shape while talking over Skype to kill the latest previous design.
The next was to look for the manufacturing partner. About one and half months later since the initial meeting with Formesa, we got an email from Rami saying that the first test piece is ready for us and they are fairly okay. With a bit of both excitement and nerves we arrived at their premises in Salo in early June where it felt rather empty for the crews having summer holidays.
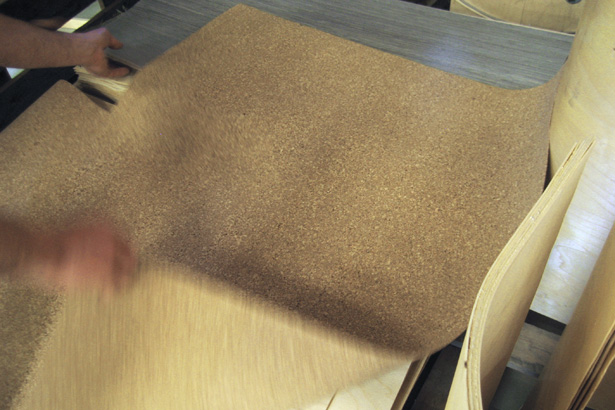
a cork sheet
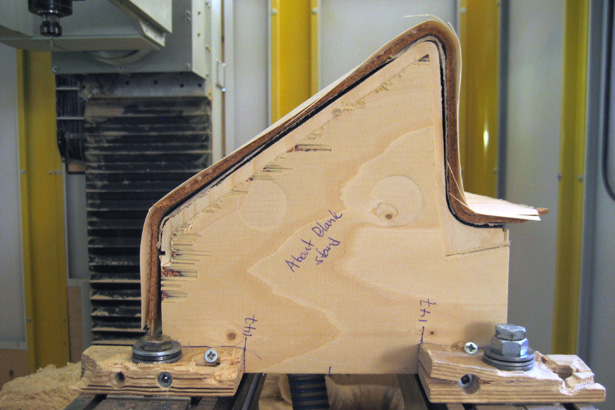
The first test mould for About:Blank Stand
There were definitely some issues. There were different thickness and colors of corks of which we had to make a decision. Though the cork layer was well pressed with other layers of wood veneer in good ones, there were many faulty pieces with ripped or burnt cork due to the heat generated while pressing. Finally, the angle we firstly designed and handed over was not versatile for different devices. We collected several models including faulty ones to test them out on our office and to learn more of the materials to give feedback to Rami. After several phone calls and emails, we made a final order to Formesa for Copenhagen Design Week.
It was in the middle of June when we heard from Rami again, and he said that our order had been executed and he confronted with rather high failure rate of over 20%. All of us had anticipated the possible of faulty products as it was the first batch and Rami had been telling us the difficulty of dealing with cork on the radically curved plywood surface, but not this much.
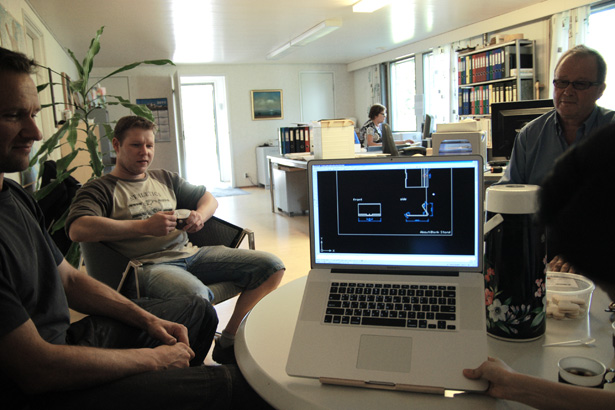
In discussion with the Aaltonens
Now, the fair was good and we are back here in Helsinki with two choices at hands. One is, though we understand the difficulty of compressing a sheet of cork with plywood together, that we just power through to keep the same “design” as the first batch, and the other is to redesign the product all over in order to reduce the waste.
What is design anyway? It is a set of activities to resolve problems, and for us dumping more than 20% after producing is too wasteful and thus a serious problem. For now, we have concluded that we will have to work more closely with Formesa for the second batch to resolve the problem, as we believe that there is always more than one way to win the Settlers of Catan from which we all the time learn about life.